Mechanical Equipment in IED Clearance:
Observations from Iraq
CISRThis article is brought to you by the Center for International Stabilization and Recovery (CISR) from issue 25.2 of The Journal of Conventional Weapons Destruction available on the JMU Scholarly Commons and Issuu.com.
By Pehr Lodhammar and Mark Wilkinson, Ph.D. [ United Nations Mine Action Service (Iraq) ]
Mechanical equipment has been in the inventory of conventional military forces for the purposes of military engineering—including demining—since the Second World War. The integration of mechanical equipment into the United Nations Mine Action Service (UNMAS) Iraq clearance activities may have therefore seemed a natural evolution from what might be considered ‘conventional’ mine clearance, yet it brought with it a number of issues. First, the absence of any clear doctrine for the use of mechanical equipment in improvised explosive device (IED) clearance generated resistance and criticism from specialist IED clearance companies operating at that time in Iraq. It was argued that mechanical operations were not only at odds with the principles and philosophies of IED disposal (IEDD) then used, but that they were also dangerous. Second, those same companies argued that the use of mechanical equipment would be extremely limited—largely to ‘shifting and dumping’ rubble and other detritus. Finally, it was argued that manual teams were quicker, more flexible, and cheaper. While UNMAS pushed ahead with the integration of mechanical equipment into standard clearance team structures, it did so in a carefully considered way. Analysis and evaluation has shown a clear role for mechanical equipment in IED clearance, albeit with some key factors that must be carefully considered. These include assessments of likely IED types and main charges as well as quantities present, the proximity of people, buildings, and secondary hazards as well as the original ground level and composition. A critical analysis of the most common concerns cited over the use of mechanical equipment in IED clearance provides ample evidence that not only can mechanical IED clearance be conducted safely, but it also offers some key advantages over manual activities.
The use of mechanical assets in the clearance of explosives from the land is nothing new. While not used in the field of humanitarian mine action (HMA) until the early 1990s, mechanical equipment had been in the inventory of many countries’ military minefield clearance units since 1942.1 By 2004, a detailed Geneva International Centre for Humanitarian Demining (GICHD) study of mechanical applications in demining had identified thirty-five machines designed and developed specifically for that purpose.2 Without exception these machines were intended for the clearance of conventional minefields, yet their application was less than perfect. Criticisms included them sometimes throwing mines into cleared areas, failing to detonate mines, burying mines deeper in the ground, as well as opinions that the machines were less than optimal in operational use because of the costs associated with purchasing and running them.
By 2015, in the face of IED contamination following the Islamic State of Iraq and the Levant (ISIL) occupation of parts of Iraq, it was clear that trying to tailor even an emergency response to the most immediate need for clearance required novel and innovative approaches demanding specialist skillsets and procedures different from those seen in a “normal” mine action program. While UNMAS Iraq quickly and successfully deployed multiple clearance teams across the liberated areas of Iraq reaching Mosul even as fighting continued, it was clear even in the earliest stages of response that the sheer volume of rubble, partially-demolished buildings, and other battle detritus in areas requiring clearance meant that there was a need for mechanical support. It was also clear that neither the necessary doctrine nor working practices existed to effectively use these machines in the delivery of IED clearance activities. This was the start point from which UNMAS began to develop its understanding of the role of mechanical assets in IED clearance.
The Basics
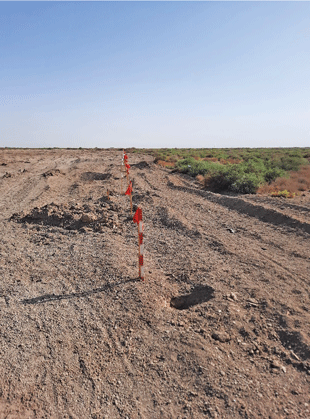
A good example of the environmental impact of conventional mechanical demining. The right of the picture represents ‘before’ and the left ‘after.’ The exposure of top soils and removal of vegetation is obvious.
In order to consider the integration of mechanical assets into IED clearance plans, one must first accept two key points. First, regardless of whether they are cleared manually or mechanically, IEDs are an explosive hazard (EH): As long as they are safely removed, the methodology used to achieve this does not matter. Second, there is no need to recover either complete IEDs or component parts for evidential (or any other) purposes. If, for example, IED components are forcefully separated during clearance, it does not matter—again, they just need to be safely removed. The sheer scale of contamination in Iraq dictates that IEDs should also be removed quickly. Mechanical options for clearance therefore potentially have clear advantages over other manually-based methods.
So What is the Problem?
In the early stages of the UNMAS emergency response in Iraq, it was apparent that “traditional” mine action actors simply did not have the skills and capacity to conduct IEDD on a massive scale in a “high threat” environment. In most cases, the only individuals trained to a high enough standard to conduct IEDD activities within this environment came from military forces, and almost without exception, western militaries. As a result, the emergency response that UNMAS initially required came from commercial companies that were arguably more quasi-military than civilian due to their largely ex-military staff, most with little or no experience in HMA.
In the absence of applicable International Mine Action Standards (IMAS) or any other HMA-based IEDD doctrine, these companies developed their own operating procedures that in some cases were little more than a “cut and paste” of military ones. In Iraq, the government forbade the importation or use of explosives by commercial organizations. This, along with operating locations often littered with rubble and debris, made the use of costly explosive ordnance disposal (EOD)/IED robots non-viable. As a result, the semi-remote separation of IED components—where a disposal operator manually connects tools to render safe the device, operating them from a distance (normally by rope)—became ubiquitous. This method satisfied the need for “remote actions where possible” that was entrenched in most military IEDD doctrines, and circumvented the requirement for disruptors or other explosive render safe tools. It was clear that there was simply no incentive for these companies to attempt to develop a sophisticated role that went beyond shifting and dumping of materials with mechanized equipment. Why would they when maintaining large, international-staff-heavy organizations and manual-team methodologies justified high-value contracts?3 The reluctance of international clearance contractors to integrate mechanical equipment into their clearance methodologies was a significant obstacle, both in terms of gaining acceptance of the value of this equipment, and in identifying and integrating the correct skillsets in projects dominated by traditional IEDD operators. Some senior IEDD experts even publicly argued that mechanical assets could not, and should not, be used for clearance of IEDs.
What Changed?
As the emergency response phase transitioned into a stabilization and then a humanitarian one, changes to the structure of commercial contracts slowly opened the door for international nongovernmental organizations (INGOs) to enter the Iraqi clearance “market.” As they arrived, they brought with them not only new perspectives on IED clearance drawn from their extensive experiences in (not-for-profit) humanitarian demining elsewhere in the world, but also their different methodological approaches, which made significant use of mechanical assets. In addition, while UNMAS had, from the outset, defined a role for mechanical support to clearance, this now presented the opportunity to begin developing specific clearance methodologies for IED environments.
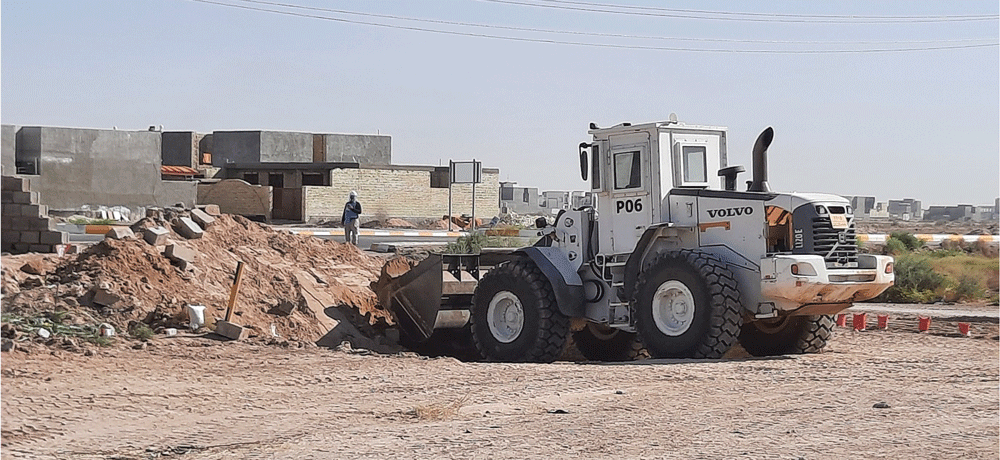
An armored front-end loader demonstrates rubble removal on a training task.
The Operational Use of Mechanical Equipment
The use of mechanical equipment in Iraq has followed a pathway of evolution, responding to operational requirements, available funds, and the development of operating procedures. Without exception, UNMAS Iraq projects have utilized front-end loaders and long-arm excavators, always with armor protection for the operator and task-specific attachments (such as rakes). In general terms, the main uses addressed are:
- Access. Commonly within urban areas to clear roads and access routes of rubble and detritus in order to reach task locations and clear incident control points (ICPs), facilitating vehicle movement.
- Rubble. Clearance of rubble within a task location, normally including rubble removal and spreading out rubble for manually checking before moving the rubble off site/recycling.
- Ground clearance/proving. More common in rural areas to clear access lanes for technical survey (TS), subject to threat assessment.
- IED location. Normally within rural environments with the aim of visually locating IEDs while moving rubble/earth.
- IED render safe/removal. Using mechanical equipment to separate an IED into its component parts and removing it from its emplaced position into a safe area.
- While there are multiple possible roles for mechanized equipment, their use is not straightforward, and a number of factors affect and influence deployment.
The Main Considerations
The integration of mechanized equipment within IED clearance operations is not just influenced by the environmental context, nor by the operational objective of their use. Cost of equipment is and remains a significant consideration in clearance activities. Much like an aircraft parked on a stand, if mechanical equipment is not being used, it still costs money; and worse, the environment of Iraq quickly degrades equipment parts, such as hydraulic hoses, due to the intense UV radiation. Planning and careful management can mitigate expensive down time, but further work is required to understand how many hours per week machines must work to justify their cost. The impact of other variables, such as area cleared, must also be included in this analysis.
A number of other factors are at play that require careful consideration, in particular within the context of risk assessment:
- Main charge type/size. This is perhaps the single most important consideration prior to deployment. Where the risk of blast effect from the unintended initiation of the most commonly found plastic-cased main charges may be acceptable in terms of the level of operator protection provided, for heavy-cased, metal, main charges (such as artillery shells) it may well not be. While the main charge container is an important consideration, so too is the weight and type of explosive fill. An ammonium nitrate–based explosive will clearly have a lower velocity of detonation and therefore less brisance than, for example, a commercial RDX- or HMX-based explosive.4 A further significant consideration is in areas where shaped charges are present; the consequences of a directional impact, even on armor, is likely to be devastating.
- Proximity of other devices. Where mechanized equipment is used for IED location/render safe/removal in IED belts, careful consideration must be made in terms of the proximity of other devices, and in particular the possibility of propagation of an explosive event.
- Proximity of people/buildings. As with all IEDD activities, careful consideration should be made to any cordon required to protect persons or property from the events of an unintended explosion.
- Location of secondary hazards. Often neglected in clearance planning, it is arguably more important to consider secondary hazards in post-conflict environments than in other home security IEDD environments. It is often the case that flammable materials as well as other explosive items litter task areas, especially within complex urban environments.
- Environmental impact. While not always a key factor for consideration in planning, the environmental impact of mechanical clearance activities should be considered. While further research is required, in particular relating to possible mitigations required, it seems clear that mechanical removal of the top soils of a location—often under windy conditions—may have negative consequences for future land use, especially agriculture.
- Weather/ground type. The effects of poor weather, in particular heavy rainfall, can obviously have a significant effect on the friction coefficient of soils, as well as the drawbar pull available to vehicles.5 That said, extreme weather also severely impacts manual clearance activities. Further research to determine at what point work should cease in the face of inclement weather is required.
- Original ground level. It is apparent from UNMAS activities across Iraq that care is required, particularly during mechanical rubble clearance, to correctly identify the original ground level in an area. The application of the clearance depth standard must be applied to the original and not the rubble ground level.
Fundamentals of IEDD Versus Mechanical Clearance
An initial glance of the United Nations IED disposal (UNIEDD) standards would seem to directly challenge the use of any mechanized equipment in IED clearance operations.6 Indeed, these standards do not even consider the use of mechanical equipment for IEDD. In terms of the principles of IEDD, a number of them are clearly directly at odds with the use of mechanical equipment; “remote means where possible” and “minimum time in target area” would seem to be the most obvious contradictions.7 Additionally, and certainly within the context of UNIEDD standards, mechanical equipment operators are ordinarily not IEDD or even EOD trained, suggesting it would seem to be impossible to integrate mechanical equipment into clearance operations at all. In order to rationalize this juxtaposition, one must compare the predominant opinions on the use of mechanical equipment in IED clearance with the reality of what the evidence gathered by UNMAS during mechanical IED clearance activities in Iraq to date actually suggests:
EXPERIENCE SAYS victim-operated IEDs (VOIEDs) require specialist IEDD operators to safely conduct render safe procedures.
EVIDENCE SAYS no, mechanical equipment operators have been successfully trained to recognize unexploded ordnance (UXO) as well as IEDs and their component parts to a level sufficient to recognize and render safe IEDs. Almost without exception, mechanical equipment is used successfully and exclusively against VOIEDs.
EXPERIENCE SAYS the use of mechanical equipment against VOIEDs will cause high numbers of unintended initiations of devices.
EVIDENCE SAYS not true. For one implementing partner working with UNMAS in Iraq and surveyed during this research, there were zero detonations (partial or full) out of a total of 1,299 IEDs cleared by mechanical equipment since 2018 across their UNMAS-funded projects. Across that partner’s entire work completed from July 2018 to September 2021, of 3,501 IEDs mechanically cleared, there were five partial detonations—representing only 0.1428 percent of the total.8 These detonations resulted in no casualties or wider damage.
EXPERIENCE SAYS mechanical equipment is slower than well-trained manual search teams.
EVIDENCE SAYS not necessarily. In areas with mineralized earth, or excessive metal contamination, the daily productivity of mechanical clearance teams often far exceeds that of manual teams. That said, mechanical equipment needs to be carefully integrated within clearance plans. The intelligent use of TS in particular is a critical enabler for the subsequent use of mechanical equipment to its maximum effect.
EXPERIENCE SAYS the use of mechanical equipment for IED clearance will result in targeting of that equipment.
EVIDENCE SAYS not a valid comment. UNMAS is only mandated to clear legacy IEDs. To that end, UNMAS would not operate in an area where active targeting was taking place. It is true that a small number of vertically-emplaced pressure plates have been recovered from Fallujah, and that these were assessed to have been emplaced to target Iraqi Security Forces using bulldozers for clearance.9 It is assessed that current mechanical IED render safe methods would go some way to reduce the effectiveness of these devices should they function. It is obvious that standard operating procedures (SOPs) for the use of mechanical equipment in IED clearance must be regularly reviewed and sensitive to specific threats that may exist within task areas. This may mean that in certain threat environments mechanical equipment will have more limited application.
After even a superficial analysis of the opportunities to use mechanical equipment in IED clearance, the prevalence of conventional IEDD philosophy and mindsets does appear to reflect the most common preconceptions about its safe and effective use. One of the key observations and lessons drawn from the experiences of UNMAS in Iraq since 2015 is that, as an HMA community, we should be constantly encouraging and searching for innovative and new techniques in order to conduct clearance more safely and effectively. Any assessment of the clearance techniques applied within HMA environments should be evidence-based, not prejudiced by the experience of IEDD operators (in particular) trained within military forces. The reality of the evidence currently available suggests that mechanical equipment can play an integral part in large-scale IED clearance.
The Future of Mechanical IED Clearance: Further Discussion Needed
The analysis presented here appears to warrant further development work to continue to effectively and safely integrate mechanical equipment into IED clearance projects. That said, a number of issues do require further focus:
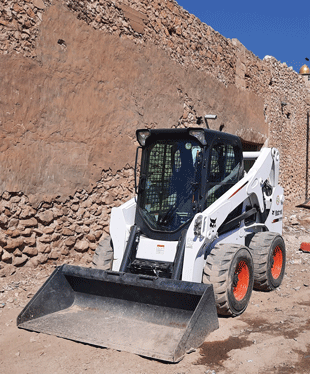
Non-armored equipment such as this Bobcat has been utilized to enhance clearance activities in confined and cluttered spaces.
Definition of role. Mechanical equipment brings clear advantages to IED clearance operations but is not a panacea. Careful consideration of its expected outputs must be made at the planning and procurement stages. The front-end loader and long arm excavator have become quite ubiquitous on UNMAS Iraq projects, but there are opportunities to add other equipment types. UNMAS Iraq has experimented with smaller equipment such as the “Bobcat,” and results so far appear encouraging. Any mechanical equipment used in IED clearance must be decided based upon a clear requirement, not merely the claims of manufacturers that their specific pieces of equipment are effective.
- Integration. Evidence so far suggests that this equipment must be integrated with clearance teams in a comprehensive way. Effective use of mechanical equipment is the result of intelligent task management. The use of TS is critical in maximizing output. In addition, careful consideration must be given to the type of follow-up activities required for quality control (QC) and quality assurance (QA) processes.
- Cost-effectiveness. It is easier to predict the cost of clearance with mechanical equipment (per square meter) than it is for manual clearance activities, not least because the mechanical rate is consistent against multiple variables that affect the progress of manual teams.10 These indicative costs have broader utility in better budget-centered procurement. That said, when mechanical equipment is contracted, it is vital that it be fully utilized to prevent parked-up costs escalating. The creation of pools of equipment shared across multiple projects may be an option to facilitate this.
- As an enabler. If mine action activities are an enabler of subsequent development, in particular stabilization activities, then it seems clear that the presence of mechanical equipment on clearance sites offers other knock-on benefits. These could include wider area clearance, rubble recycling, and other civil engineering works (to include excavation for reinstatement of services). Careful analysis of the specific needs of a clearance area could demonstrate considerable cost and time savings through a more joined-up approach to meeting the stabilization and other needs of the work area.
- Clearance versus civil engineering. There is the possibility of a considerable lack of clarity between what mechanical equipment contributes when working in IED clearance and when that activity becomes civil engineering activity (for example in demolition). On a small scale this may not be problematic, but where specialist work (e.g., the breaking of concrete slab, cutting of reinforcement bar, and demolition and removal of structures) is necessary in order to give an assurance of the absence of EH in a specific task area, careful management is required. This is not just to exploit opportunities for possible enabling activity but also to ensure specialist equipment is budgeted and available along with personnel with the correct technical training and experience needed in order to ensure safe and effective work delivery.
- Specifications for armor. Regardless of the operational methodology used in mechanical IED clearance, the specifications for the armor applied to mechanical equipment does require further research and direction. In particular, consideration is required relating to the protection offered against metal-cased main charges, fragmentation, and blast/heat effects. There is a definite lack of information currently available on testing of armored equipment against IEDs.
- International standards. There is a strong case for the need to better integrate guidance on the mechanical clearance of IEDs into both IMAS and UNIEDD guidance. An initial technical note could be extremely valuable. This work should include careful considerations on the specific requirements for QC, in particular with regards to depths of clearance in rubble against original ground levels.
Final Thoughts
The work of UNMAS in Iraq has shown there is an important role for the use of mechanized equipment in IED clearance. While UNMAS has attempted to drive an evolution in the integration of mechanical equipment into IED clearance teams, there is clearly a need for the formalizing of thought in its use as well as producing subsequent authoritative guidance.
Unintended initiations of devices are sadly inevitable when conducting IEDD on the scale of clearance activity in Iraq; however, within a carefully considered risk-management process, evidence gathered by UNMAS Iraq to date suggests that survivability for operators contained within armored equipment is far higher than those conducting manual actions on devices. This is not to say “one size fits all” for the use of mechanical equipment, but where would you rather be when a 20 kg main charge functions—8 m away in an armored cab or 50 cm above the point of detonation?
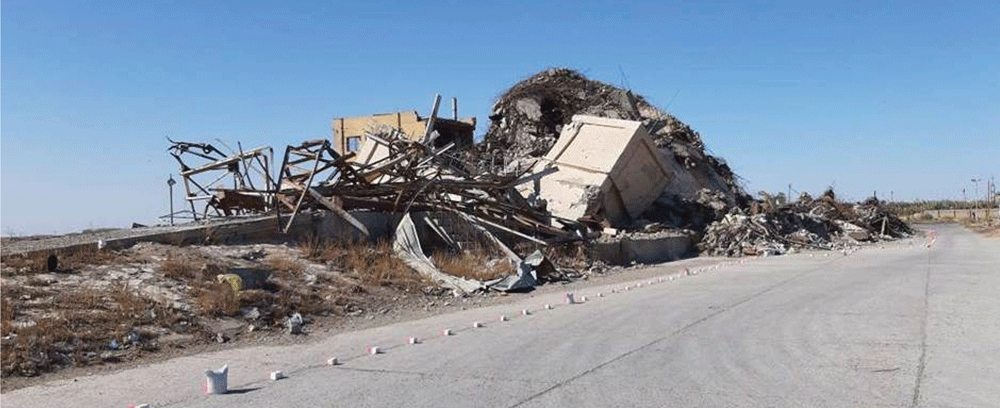
The collapsed grain silo in Ramadi, Iraq, provides an excellent example of the blurred boundary between using mechanical equipment for IED clearance and civil engineering (demolition) works.
This is not to say “one size fits all” for the use of mechanical equipment, but where would you rather be when a 20 kg main charge functions—8 m away in an armored cab or 50 cm above the point of detonation?
Pehr Lodhammar
Chief Mine Action Programme
United Nations Mine Action Service (Iraq)
Pehr Lodhammar is currently the Chief of Mine Action Programme for UNMAS in Iraq. He has over twenty years of experience in humanitarian demining operations with extensive experience in using mechanical assets in clearance. He has provided the leadership for the evolutionary processes described in this article.
Mark Wilkinson, Ph.D.
Senior Operations Manager
United Nations Mine Action Service (Iraq)
Mark Wilkinson, Ph.D., is the Senior Operations Manager for UNMAS in Iraq. He has twenty years of professional experience in military and HMA. As a former British Army Ammunition Technical Officer, he worked as a High Threat IEDD Operator in several operational environments before transitioning to HMA. He has an active research agenda focused around IED clearance in HMA environments.